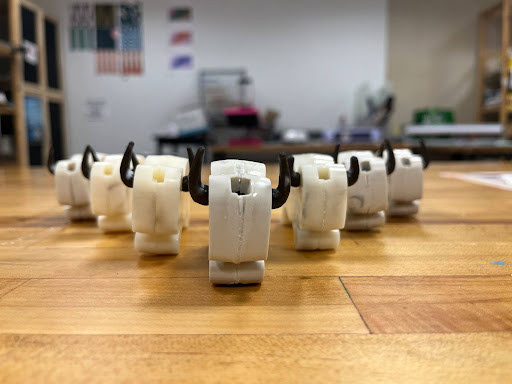
In this project I learned all about conducting the injection molding process by designing and manufacturing a functional small whistle that could be mass produced. The bison whistle is inspired by the Aang's whistle from Avatar the Last Airbender which he uses to call Appa. The whistle is based what it looks like in the show where it is a 2d outline of Appa with two horns. This was the final project for my Design for Manufacturing class, and the goal was to make a cool toy that was true to the source material. The resulting whistle looks fantastic and works great!
Components
There are 4 main parts in the assembly. Two a top and bottom half of the body as well as the two horns. The two halves of the body are located onto each other uses loosely toleranced pins, and the horns are press fit into the main body of the part. Additional cavities where added to the body to avoid sinking.
Prototyping
Various whistle geometries where prototyped to find one that would make a clear and distinct whistling sound. It was determined that having sharp angles to compress the air flow was critical to the whistle making a proper sound.
Flow Modelling
After finishing part design, flow analysis was conducted on the part using Solidworks Flow Simulation. This predicted the flow time for the injection molding as well as confirmed that the fluid would flow properly. It showed were vent holes would be necessary and where the boundary of the flows would meet each other.
Molds
The molds were CNC milled on Tormach 3 axis CNC machines. The CAM was designed in Fusion and took 2-3 hours for each side of the mold. All of the surfaces were drafted to ensure that the molded parts would easily be removable. The runners and gates were precisely determined to allow for proper flow of the plastic. Alignment pins where used on the corners to repeatably and precicely put the two halves of the molds together. The horns required a quick pass with a 1/16th in ball end mill to get the detailed geometry and small tip. Even more detailed was the sharp corners on the whistle which was machined with a .015" tapered end mill.
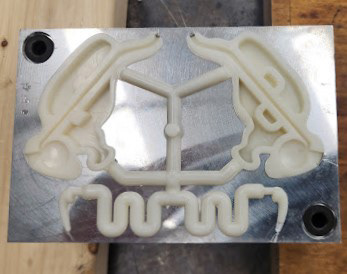
Injecting Process
The Olin Shop injection molding is not a industrial scale machine so it took a lot of fiddling to get the injection settings just right and it wasn't super consistent. This was particularly an issue since our parts were rather large for the size of the machine. However, we got some perfect shots such as the one to the left!
Three Challenges
1) For the whistle to work properly the two halves need a airtight seal between them. Originally a press or snap fit around the perimeter of the part was considered, but due to how small the part is compared to the tooling that I had access to on the Tormach's it didn't make sense. Instead I opted to add a locating feature to both sides of the body and then using acetone to chemically bond the ABS of the two sides together.
2) You may notice that the body has a cavity that extends all the way to the edge of the part. This made creating the mold parts more difficult in Solidworks since it broke the parting surfaces the Solidworks mold tools create. Instead I had to manually use the cavity tool to properly cut out the geometry needed. Additionally, from a tolerance perspective this raised a challenge as if we machined the parts without additional tolerancing the halves of the mold would have zero tolerance at those points. Another team had a similar issue and there molds wouldn't fit together requiring them to machine additional material off. To avoid this we removed an additional .002" from the walls of the cavity of the bottom mold to ensure that they would properly fit together.
3) For not entirely clear reasons the horns filled perfectly in some shots, but then wouldn't complete in others, we ended up blocking the flow paths to the two bodies and just made horns. With the smaller plastic volume the horns shot without a any issues, and could be rapidly manufactured at a of less than a minute per shot of plastic.